6 Ways to Reduce Your Injection Molding Costs
Injection moulding is a manufacturing process used universally to manufacture various everyday goods. The majority of mass-produced products contain plastic injection moulded components including furniture fixings, plastic cutlery, CCTV cameras, games consoles, toasters, and vacuum cleaners.
How much does plastic injection moulding cost?
First of all, a basic question, what is the cost of mold. Many people think that cost of the mold is mold material fee + processing fee + tax, of course, labor and design fees, but we can think that labor cost includes in processing fee.
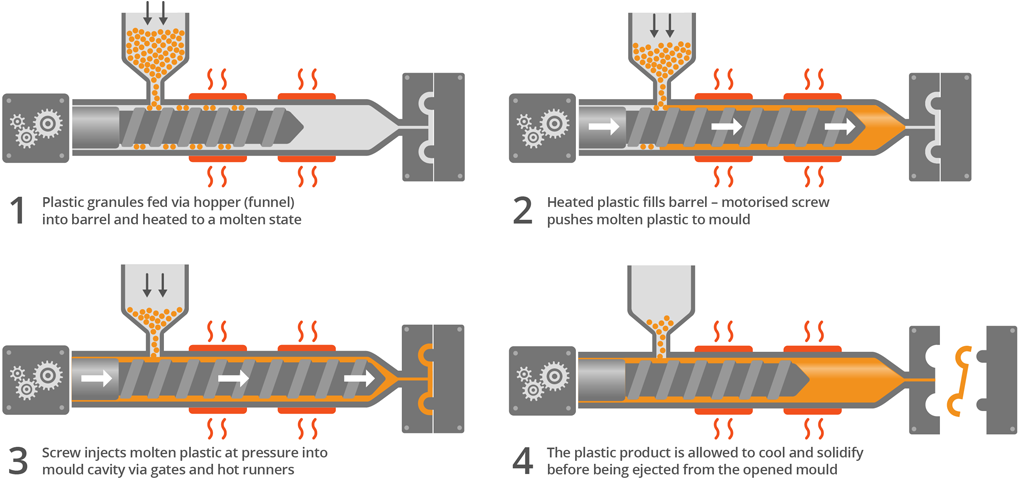
6 Ways to Reduce Your Injection Molding Costs
How to reduce the cost of mold?
The price of injection moulding varies with every project. Due to the initial upfront cost of the mould and tooling, the greater the number of parts being produced, the lower the overall unit costs. This is because tooling costs can be absorbed across more parts. Mass-produced parts often use injection moulding as it is the most economical and timely way to produce plastic parts at high volumes.
From a narrow point of view, this answer is good, but if it is only this, then in addition to cutting corners and tax evasion, is there any way to control or reduce costs?
Ways to reduce costs in injection moulding
There are several main cost drivers with injection moulding projects. Consequently, there are methods and best practices you can apply to reduce the costs of injection moulding for a more cost-effective solution whilst still providing excellent results.
Larger production runs can be beneficial in that they can benefit from economies of scale which reduce unit costs. However, depending on budgets and requirements, larger production runs may not be suitable as they often result in surplus stock and waste. If you are looking for further ways to reduce costs in your injection moulding project, this guide analyses injection moulding costs and offers solutions and ways to save money throughout the injection moulding process.
Injection moulding costs are determined by various factors, including:
- Optimize Part Design: The design of the part being molded has a significant impact on the cost of the injection molding process. A well-designed part can reduce the number of parts required to make the product, which in turn reduces the cost of materials and production time.
- Use Cost-Effective Materials: The choice of material used in injection molding can significantly impact the cost of the process. Choosing a cost-effective material that meets the product’s requirements can help reduce production costs.
- Optimize Mold Design: The mold design is critical to the injection molding process. A well-designed mold can reduce the number of parts required to make the product and reduce the cycle time, which in turn reduces production costs.
- Optimize Production Parameters: The optimization of production parameters such as temperature, pressure, and cycle time can help reduce the cost of injection molding. Optimizing production parameters can improve the efficiency of the molding process, reducing the time and energy required to produce the product.
- Reduce Waste: The injection molding process generates waste, which can increase production costs. Implementing measures to reduce waste, such as recycling, can help reduce production costs.
- Work with a Reputable Injection Molding Company: Working with a reputable injection molding company can help reduce production costs. A reputable company will have experience in optimizing the injection molding process and can provide guidance on how to reduce production costs.