Cost of customized injection mold
Injection molding is the most common method of production, with some commonly made injection molded items including computer components to outdoor furniture.
Injection molding is a manufacturing process for producing plastic injection molds from both thermoplastic and thermosetting plastic materials. Material is fed into a heated barrel, mixed, and forced into a mold cavity by a reciprocating screw or a ram injector. Where the injection molded part cools and hardens to the configuration of the mold cavity. After a part is designed, usually by an industrial designer or an engineer, molds are then manufactured by an injection mold company. Where it is assigned to a mold maker (or toolmaker). Injection molds are usually constructed using either steel or aluminum. And precision-machined to form the features of the desired parts. Injection molding is widely used for manufacturing a variety of parts. From the smallest component to the entire body panels of cars. Injection molding is the most common method of production, with some commonly made injection molded items including computer components to outdoor furniture.
One of the most common questions we receive from customers is how much a custom plastic injection mold will cost. The truth is, there is no easy way to determine exactly what mold will cost without the specific product details. The price of injection molding is based on several interplaying factors. However, we’ll break down each of those factors to give you a better idea of what influences the cost of an injection mold.
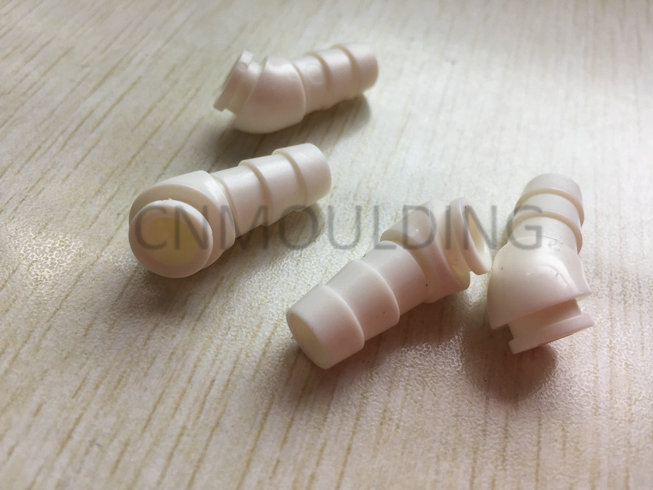
Cost of customized injection mold
How do control mold manufacturing cost costs?
First, we should choose the steel and manufacture process based on customer requirements.
After choosing the material, we should make a plastic molding company simple draft, then we will get the mold size and weight.
Manufacture cost, the manufacturing cost is 1.5-3 times of material cost based on complexity.
Every mold should consider racist cost, it normally is 10% of the mold price.
The tax depends on local policy.
The design fee normally is 10% of the total mold cost.
The trial fee is 3-5% china injection molding of the total mold price.
The way of injection mould price calculation
Mold price=steel cost+design fee+manufacture cost+profit+tax+trial cost+package and transport fee
The proportion
Material cost: steel and standard injection molding china spare part take 15%-30% mold price
Manufacture and profit: normally 30-50% of mold cost
Design fee:10-15% of mold cost
Trial fee: within 3% for big size mold,5% for a small mold
Package and transport: real cost or 3% mold price
VAT: 5%-17% of mold price
Mold control
To ensure the cost of the mold, cost control, and quality. And delivery is proportional to the relationship between the quality of the mold to do a one-time. Few changes, delivery to shorten, so that low manufacturing costs, earn high profits. A market order to undertake the process of unique competitive advantage. On the contrary, enterprises not only have no advantage but also will not make money or even lose money. Therefore, mold manufacturing costs and production management in the control part are very important, from the following aspects.
Many factors play a role in the ultimate cost of a plastic injection mold. Some of these factors include:
Tolerances
No part can be reproduced absolutely perfectly, but with proper machining, they can come close. However, as tolerances become tighter, the costs rise. Parts with relatively loose tolerances. As exterior plastics and single-piece parts are cheaper to design and produce than parts with very tight tolerances.
Mold and Cavity Complexity
The more complex the mold, the more machining, finishing, and maintenance are required. Because of this, the cost of a mold necessarily increases with its complexity. In many cases. It is more economical to design several simple molds that work together to create one piece, rather than designing a single, more complex mold.
Number of Cavities
Along with the complexity of mold cavities, you must also consider the number of cavities needed. At MDI. We recommend each mold be designed for a single part, rather than creating molds to produce multiple parts at once.
Mold Material
The first factor that influences injection mold cost is the material of the mold itself. Molds can be made of many materials to suit different needs, including standard and stainless steel, aluminum, and beryllium-copper alloys.
Every material has its own unique properties that make it more appropriate for certain types of applications. Steel, for instance, is more durable and long-lived. But also harder for the machine. Aluminum can be easily machined to very tight tolerances but doesn’t last through as many injection cycles.
Mold Base
The mold base is the larger piece that holds the separate mold cavities and other parts together in a single unit. Most mold bases are designed from standard units and then machined to your particular specifications. The number of cavities, the material of the mold and the base, and the size of the base will all play a role in the ultimate cost of the mold.
Gate Type and Placement
Gates are the points at which plastic resin is injected into the mold. There are many different types of gates available, including edge gates, hot tip gates, and sub-gates. Different types of gates are suited for different part designs. You will also need to consider the gate placement during the design phase to reduce part stress and ensure fast, even injection.
Part Material (Resin)
The material you choose for your part manufacturing will affect the design of your mold. Different resins, such as acrylic, polycarbonate, polyurethane, or PVC, require different wall thicknesses and gate and ejector pin placement to ensure optimum performance. These design considerations affect the ultimate cost of your mold.
Part Texturing
Texturing is an aspect of mold and cavity complexity. Plastic parts can be molded with a huge range of textures, but designing and machining the texture in the mold is an important consideration in the eventual cost.
Ejector Pin Number and Placement
Another design consideration for your injection mold is the ejector pins. Different pin sizes, numbers, and placements can impact your part in different ways. In general, your mold should be designed so the ejector pins minimize the stress your part encounters during ejection.
Manual Labor
Despite advances in computer drafting and automated CNC machining, manual labor still plays a role in your mold’s design. Your mold may need hand machining or finishing, or it could require several design iterations to ensure quality.
Why Choose Custom Plastic Injection Molds?
With all of these considerations, custom plastic injection molding might seem like a huge and complicated expense. However, custom injection molding does have many advantages that help offset these costs:
Part Accuracy
Only injection molding offers a high level of accurate reproducibility for large numbers of plastic parts. Other manufacturing methods can’t match injection molding for creating large numbers of parts quickly and with precision.
Durability
One well-made injection mold can create many thousands of parts over the years of use. Other methods may be better suited for short production runs, but injection molding is the most cost-effective option for long runs.
Production Speed
Injection mold manufacturing is one of the fastest ways to reproduce large numbers of highly accurate parts. Other manufacturing methods can create parts with similar tolerances, but not at nearly the same rate as injection molding.
To get an accurate quote on the cost of your own custom injection mold, reach out to a professional manufacturer with the knowledge and skills to give you exactly what you need. An experienced project manager will ensure all your requirements and needs are incorporated into your design from the outset.